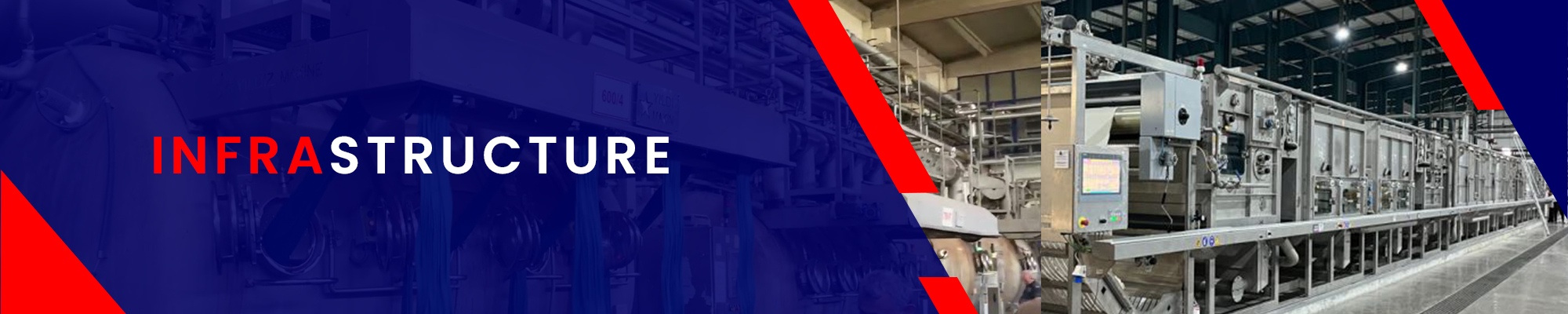
With our experts and experience we the process along the supply chain and support you along the product development and innovation at every stage from fibre to fabric.
years of Experience
20 years of experience in delivering quality with integrity and passion.
250 employees placed in the organization with safe and environment friendly work place.
Employees Placed
Tonnes Monthly
300 tonnes of monthly production full finished goods from dyeing to compacting with promising quality.
OUR PROCESS
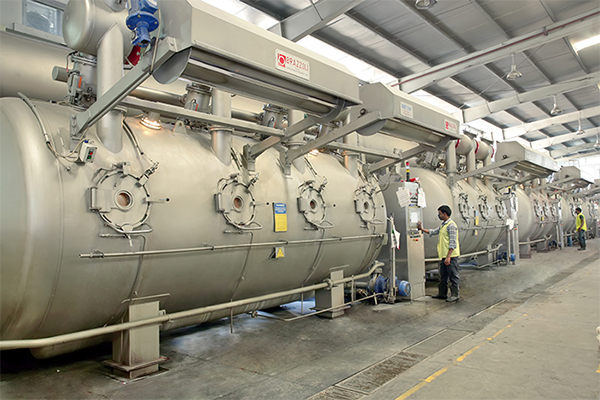
Dyeing
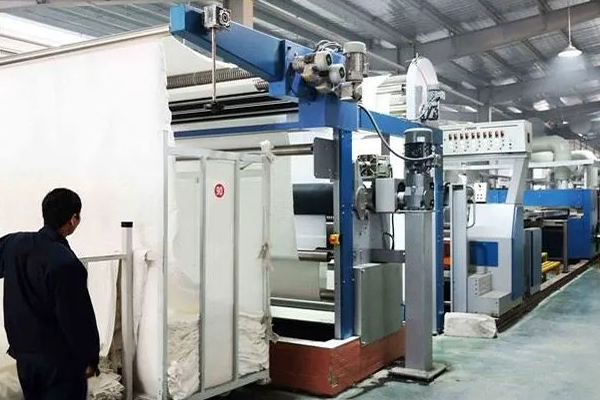
Wet processing
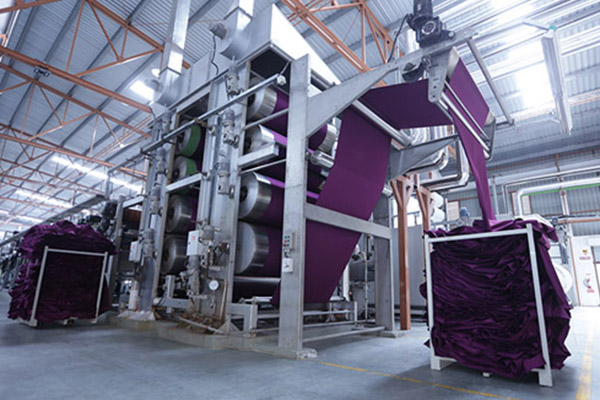
Heat setting
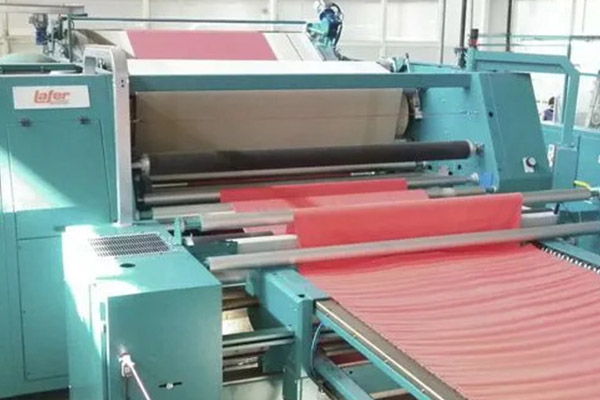
Compacting
Dyeing
We do dyeing for all sorts of fabric associated with cotton. Our quality is undeniable. We achieve the targets very easily as in back hand we really have strong automated laboratory which helps us to be so confident in our works. We are “ZLD” Unit ( Zero liquid discharge) which denote no water is left into the surface, which is again retreated and used back for the process again for eliminating all the environmental polluting factors.
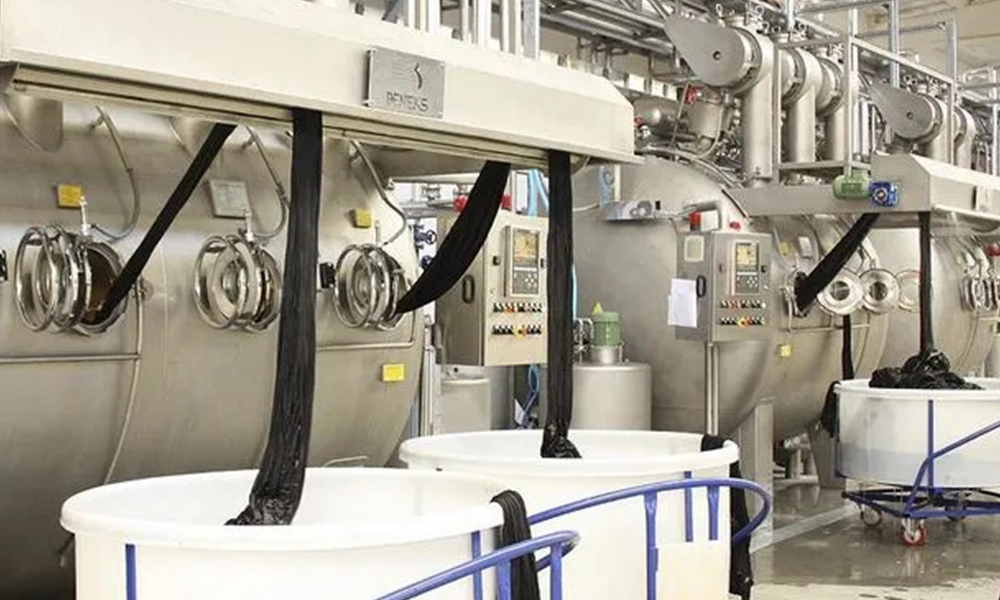
Laboratory
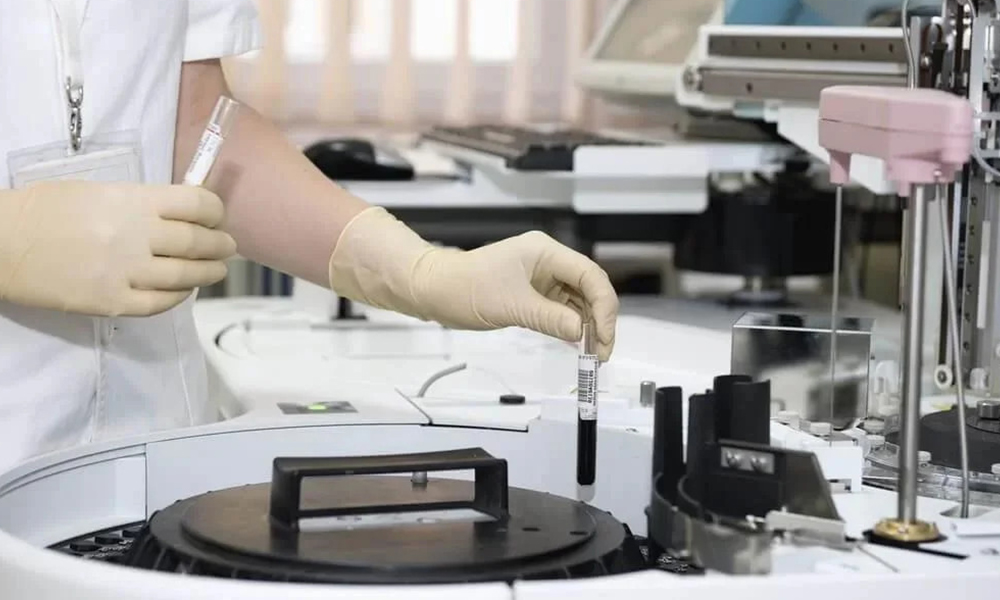
We tend to use automatic machinery for the laboratory process and to decrease the intervention of human for more accuracy. Our Automatic Laboratory Dispenser is volumetric with a very high dispensing accuracy of 0.02ml for solutions and 0.2ml for water. This is strongest base in order to achieve the target.
TUBLER HEAT SEATING
Which saves time and cost factors such as cutting and sewing of lycra and lycra blended fabrics before dyeing is designed to eliminate tension from yarn blends of raw fabric in tube form, to repair rough surfaces and to prevent fractures crease mark during dyeing.
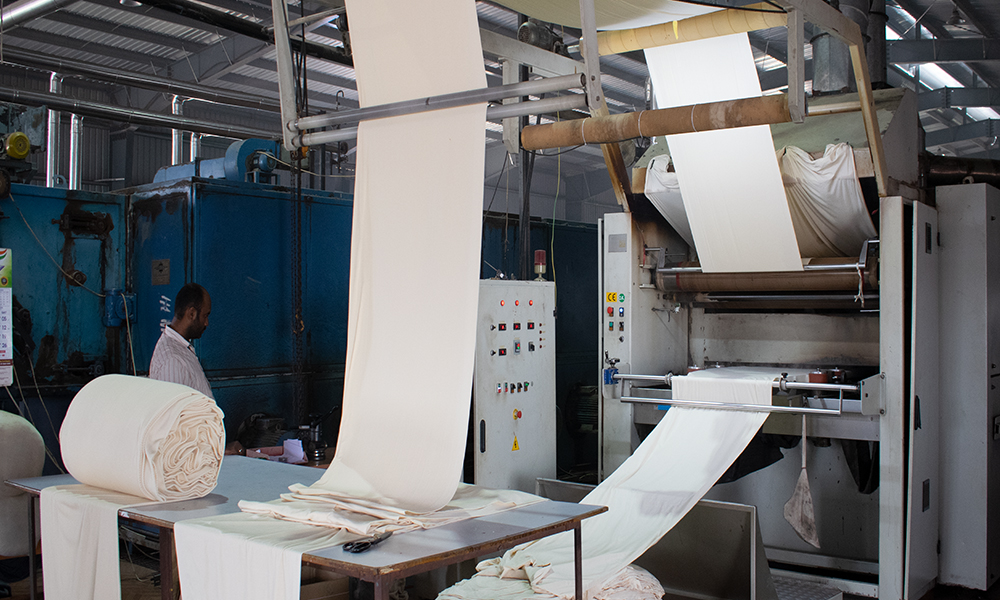
WET PROCESSING
Stentering
YOANTION-CHINA
A remarkable stenter which is highly efficient and which is assured for its quality on its fabrics where this stenter is very much special for its hand feel on the fabric because it is enable with 2 padders and at most arrest all shrinkage factors here more than any other.
This is enabled with E+L weft straightener and pinning to adjust the weft to control the spirality in the fabric.
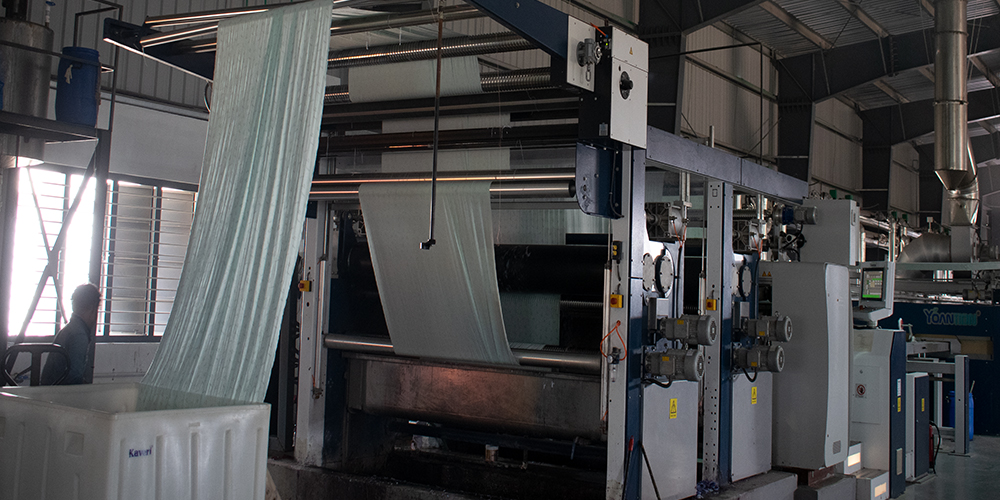
BRUCKNER – GERMANY
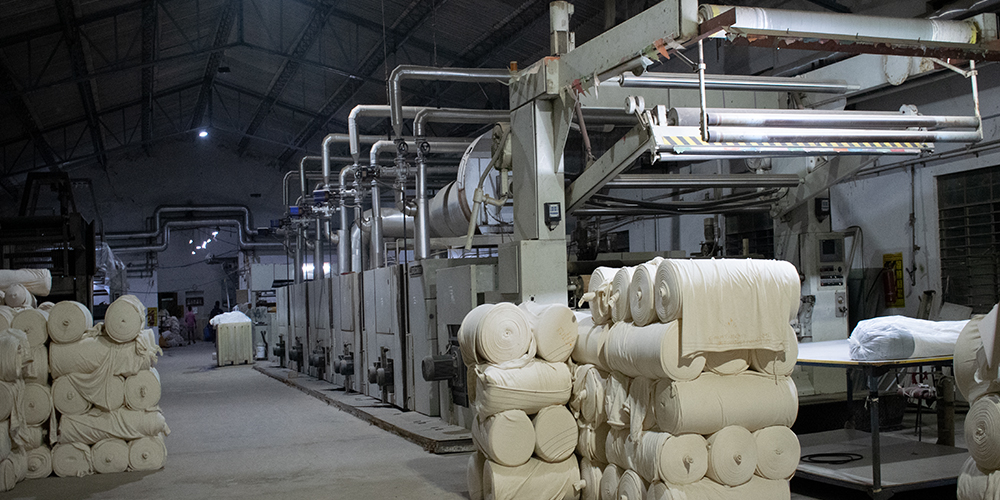
This is enabled with E+L weft A straightener which doesn’t need any introduction to the foreign market which is assured for its quality and its efficiency.
RELAX DRYER
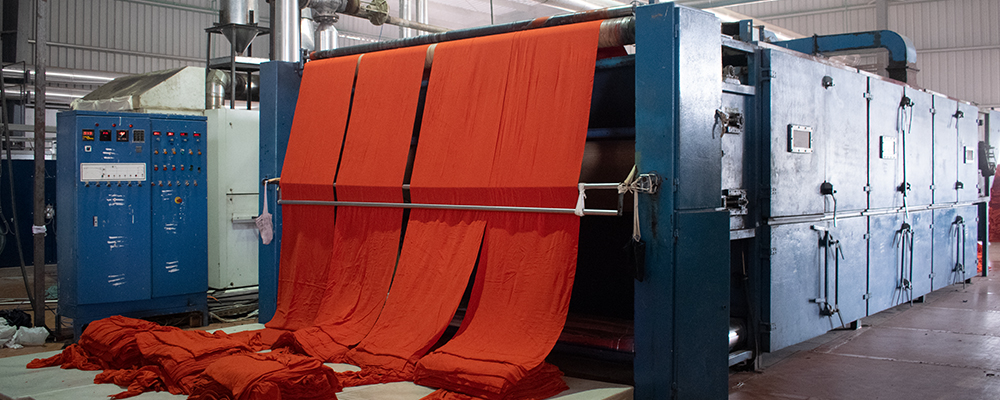
We do dyeing for all sorts of fabric associated with cotton. Our quality is undeniable. We achieve the targets very easily as in back hand we really have strong automated laboratory which helps us to be so confident in our works. We are “ZLD” Unit ( Zero liquid discharge) which denote no water is left into the surface, which is again retreated and used back for the process again for eliminating all the environmental polluting factors.
COMPACTING
Open Width – Tube Tex – USA
Open width knit fabrics with the C-2500 Open Width Compactor. The final step of processing for high quality outerwear and apparel knit fabrics will give softer hand, superior shrinkage control, width control, and yield control. Maximum compaction rates up to 25% are possible.
2 Machines
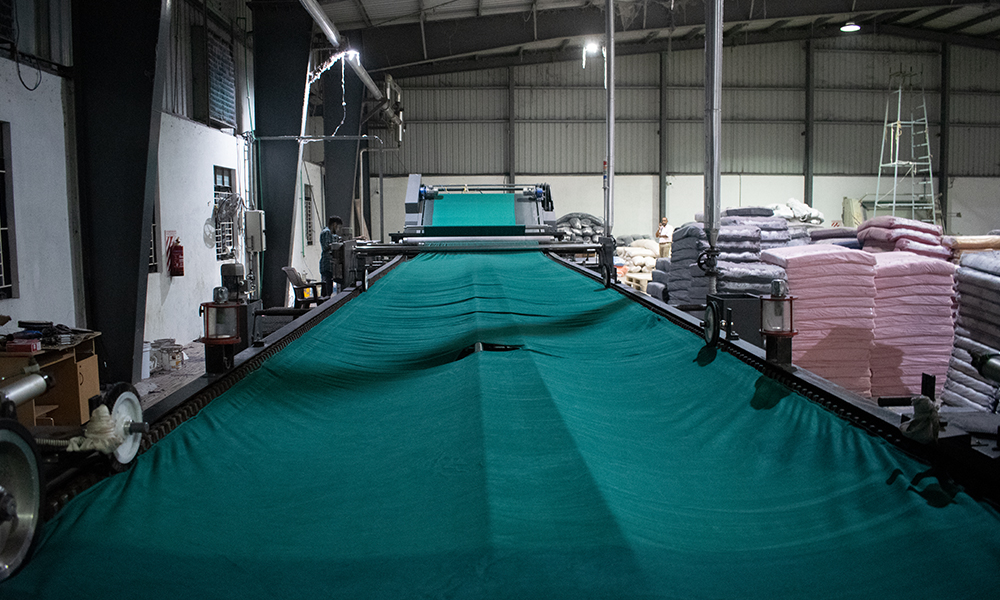
CAPACITY : 10 TONNES EACH
Open Width – Felt Compacting
Compactor felt is an endless needled felt, which is consist of polyamide, polyester and wool. It has the ability of withstand a high amount of heat during the compaction process and a very smooth surface. In the compaction unit, the knit fabric comes in contact with the felt surface. This ensure with best hand feel comparing with other sorts of compacting.
2 FEET COMPACTING
- Sintex – 2 Cylinder
- Sperotto Rimar – 2 Cylinder
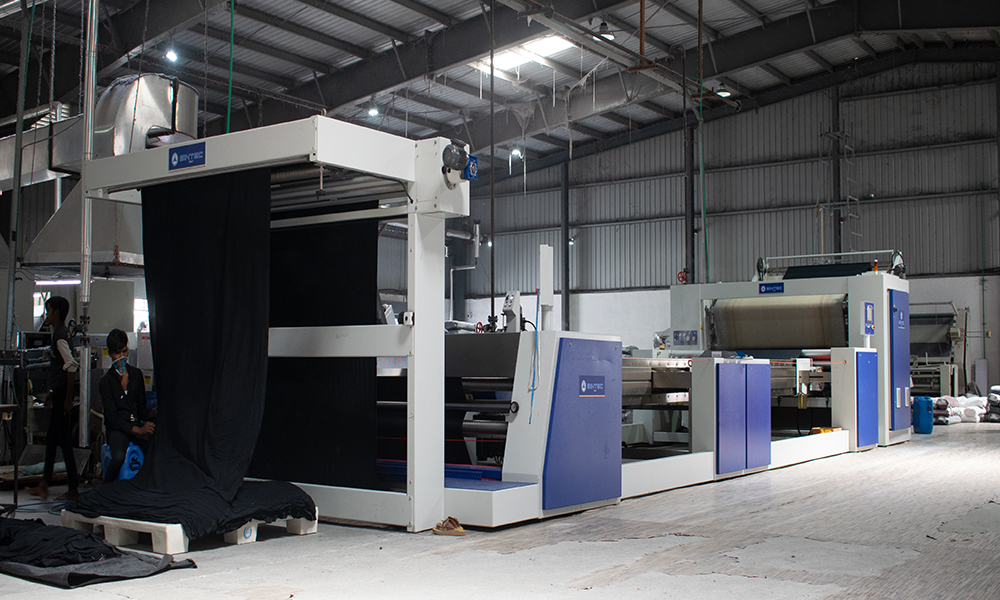
CAPACITY : 10 TONNES EACH
Tubler – Tube Tex USA
Achieve a new level of performance and appearance for tubular knit fabrics with the Navis TubeTex. For high quality outerwear and apparel knit fabrics, your facility’s final step of processing will yield a softer hand as well as superior shrinkage, width and yield control.
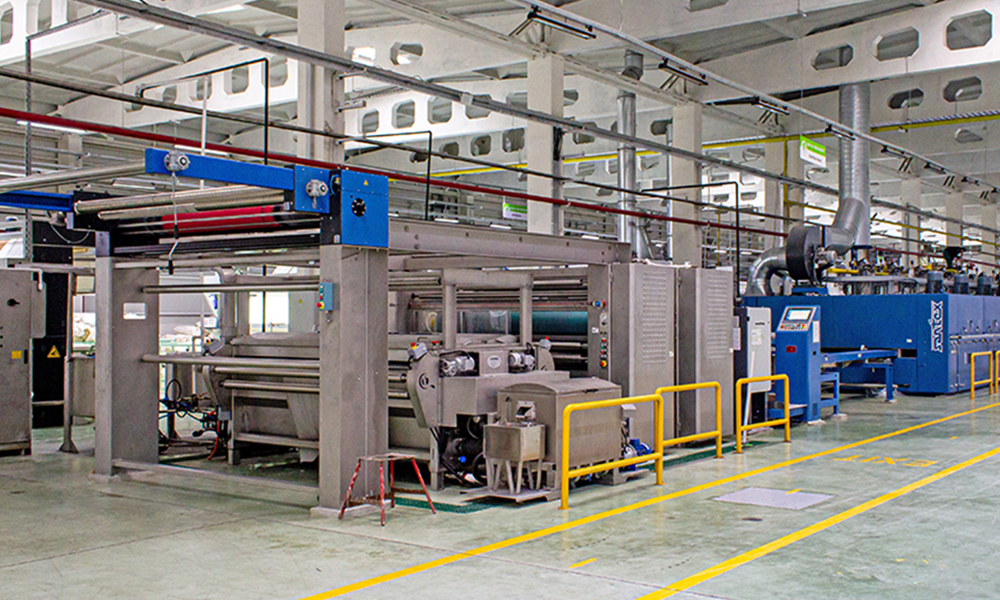
CAPACITY : 12 TONNES EACH
Ferraro Tublar Compactor
Tublar felt compactor is a felt compacting machine for finishing of tubular knitted fabrics in precision folds and/or rolls, with control of the dimensional stability.
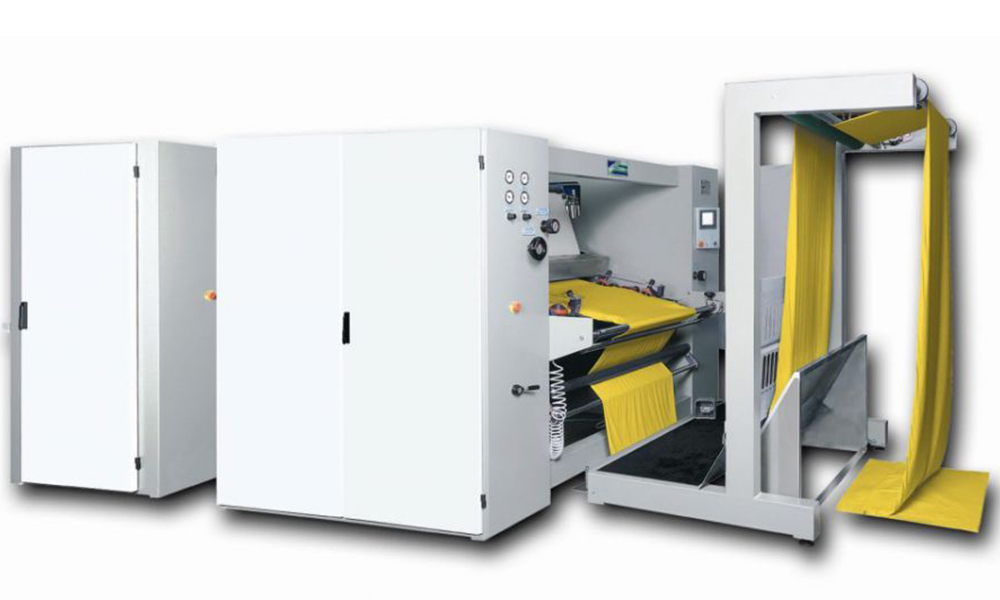
SUEDING
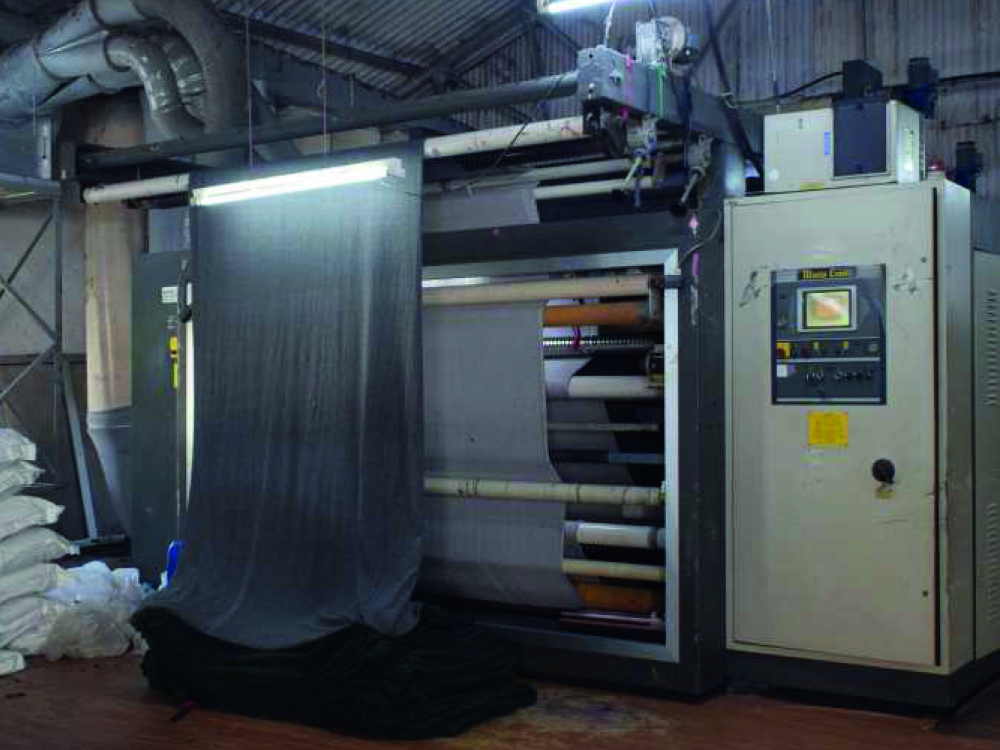
Sueding is a mechanical finishing process in which a fabric is abraded on one or both sides to raise or create a fibrous surface. This fibrous surface improves the fabric appearance, gives the fabric a softer, fuller hand, and can mask fabric construction and subdue coloration.
RAISING

Raising. Another finishing process is raising. During raising, the fabric surface is treated with sharp teeth to lift the surface fibres, thereby imparting hairiness, softness, and warmth, as in flannelette.
CAPACITY : 10 TONNES EACH
GARMENT WASHING
Garments washing are the process applied to remove the sizing of the fabrics to obtain the desired colours and effects, to ensure wearable cleanliness and to obtain wearable softness.
The process which is used to modify the appearance, outlook comfort ability and fashion of the garments is called garment washing. It is normally done after stitching. Wash types usually depend on the product nature and its using.
Types of Washing Done
- Hot Wash
- Softner Wash
- Silicon Wash
- Panel Wash
- Dip Wash
- CPL Wash
- Bio Wash
- Stone Wash
- Enzyme Wash
- Acid Wash
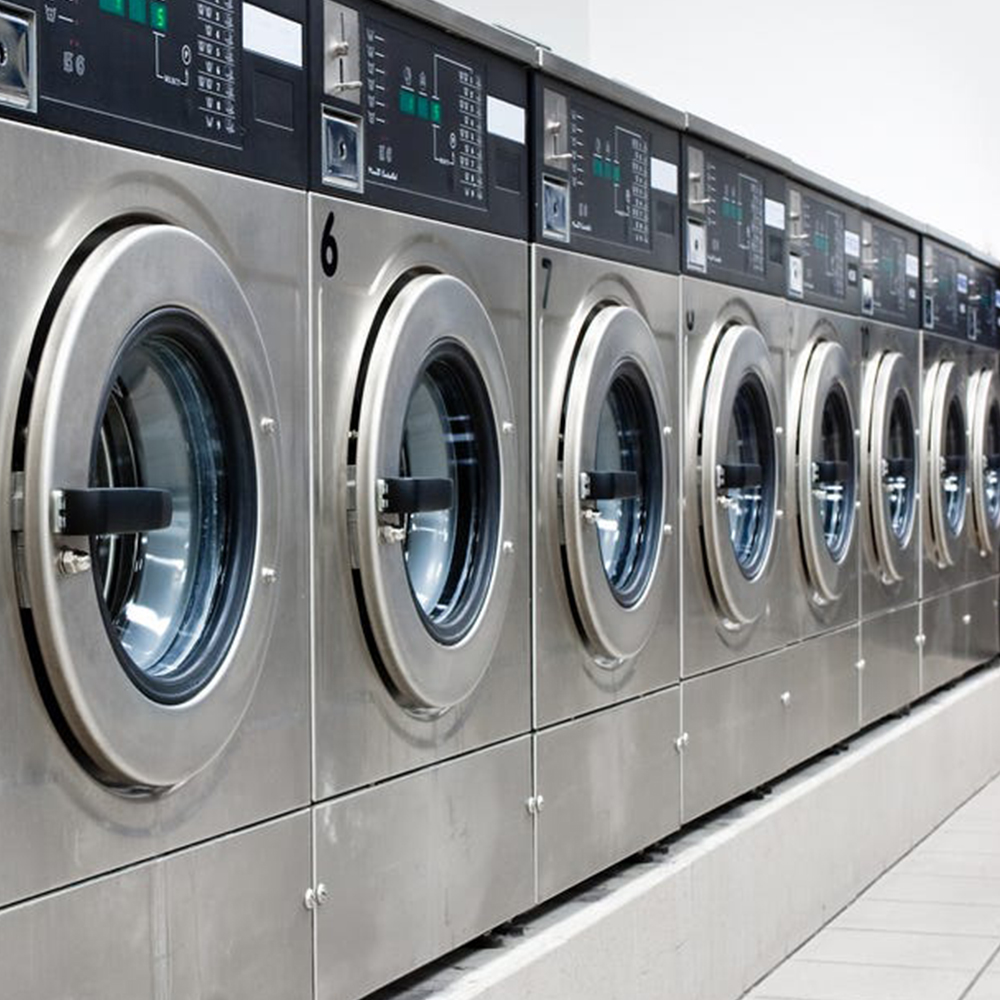